In today’s competitive automotive industry, cost-effectiveness is key when selecting reliable components for manufacturing and repair. When it comes to brake master cylinders, China brake master cylinder products have gained widespread recognition for offering the best value without compromising on quality. But why are Chinese brake master cylinders considered the most cost-effective?
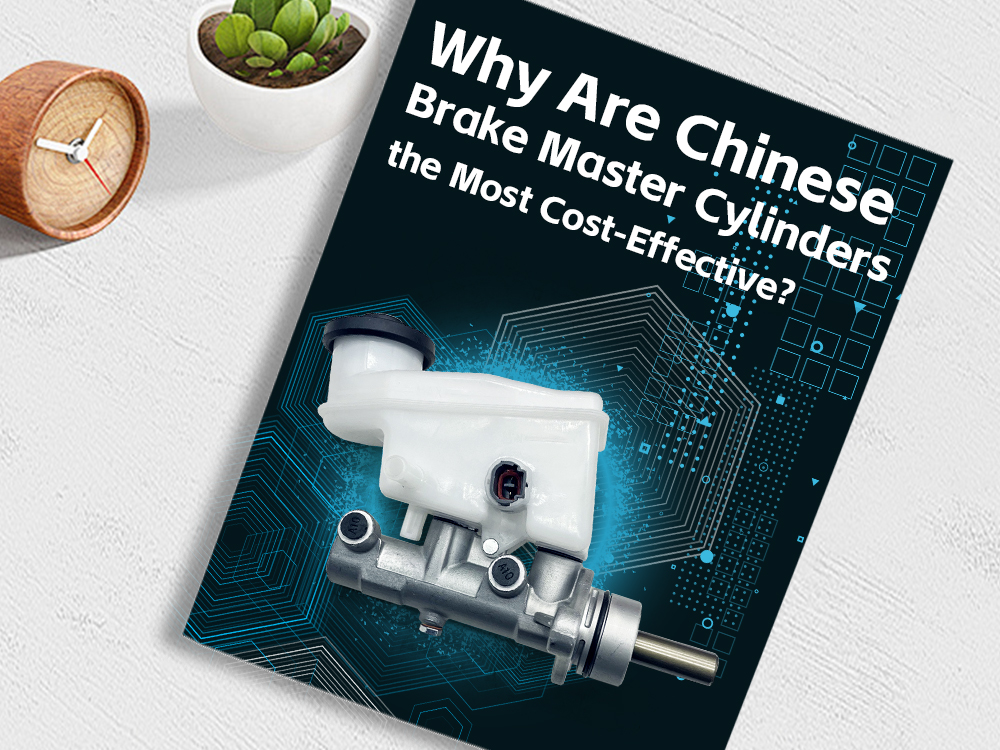
China has long been known for its advanced manufacturing capabilities, and the supplier brake master cylinder sector is no exception. The country’s factories benefit from well-established supply chains, skilled labor, and economies of scale that help keep production costs low. By streamlining the entire manufacturing process, from raw material procurement to final assembly, Chinese manufacturers are able to offer brake master cylinders at a fraction of the cost of competitors in other regions.
2. Affordable Materials Without Compromising Quality
One of the key factors that contribute to the cost-effectiveness of China brake master cylinder products is the use of high-quality yet affordable materials. Chinese suppliers are known for sourcing materials efficiently and making use of advanced technologies to optimize production. Whether it’s durable aluminum alloys or reliable rubber seals, manufacturers ensure that each component is built to last while keeping the production costs low.
3. Flexibility and Scalability
Another reason Chinese brake master cylinders are highly cost-effective is the ability to scale production according to the needs of the market. China supplier brake master cylinder manufacturers have the capability to produce both small and large quantities, catering to both original equipment manufacturers (OEMs) and the aftermarket. This scalability ensures that businesses can adjust orders to meet demand while keeping prices competitive.
4. Streamlined Logistics
China’s robust logistics infrastructure further adds to the cost-effectiveness of brake master cylinder production. With established trade routes and modern transport networks, China supplier brake master cylinder companies are able to deliver products worldwide at lower shipping costs, helping customers maintain low overheads.
Take KOMP as an example, it is a brand of wuhu Compass Auto Parts Co., Ltd., located in Wuhu City, Anhui Province, China, along the Yangtze River. With excellent water transportation conditions, it is convenient for goods to directly reach international ports such as Shanghai through the Yangtze River. Secondly, it has a high manufacturing foundation, and Wuhu is one of the important automobile parts production bases in China, forming a large-scale and clustered production mode. High production efficiency and collaboration rate. Having a complete supply chain from raw materials to finished products reduces import dependence and lowers costs. And the labor cost is also low, the production cost is low, and the product quality is high, which makes KOMP's brake master cylinders produced in China have most cost-effectiveness.